
If you continue to browse, scroll, click or otherwise interact, you are providing implicit acknowledgement and agreement to this.Ĭopyright © 2002-2022 Aircraft Engine Historical Society, Inc. This website depends on cookies to make it function. The Westinghouse J34, company designation Westinghouse 24C, was a turbojet engine developed by Westinghouse Aviation Gas Turbine Division in the late 1940s.Essentially an enlarged version of the earlier Westinghouse J30, the J34 produced 3,000 pounds of thrust, twice as much as the J30. With questions or comments about this web site. Photographed at the US Air Force Museum on January 15, 2000 Steam enters the main turbine at the high pressure turbine through the turbine stop (throttle) and control (governor) valves. Shown are the dual drive shafts and separate gearbox used in the Fisher P-75A Eagle A cross-section of the turbine is shown in Figure 7.4-1. Normal thrust, flight: 465 lbf (2.The National Museum of the United States Air Force (Formerly The US Air Force Museum), situated on the Wright-Patterson Air Force Base near Dayton, Ohio,is the "oldest and largest military aviation museum in the world." Military thrust, flight: 525 lbf (2.34 kN) at 18,000 rpm at altitude Normal thrust, static: 1,170 lbf (5.20 kN) at 17,000 rpm at sea level Specific fuel consumption: 1.28 lb/lbf/hr (130.48 kg/kN/hr) Maximum thrust: 1,400 lbf (6.23 kN) at 18,000 rpm at sea level

Normal thrust, flight: 570 lbf (2.54 kN) at 16,260 rpm at altitude The first ones were being manufactured for aircraft by. This is what everyone in the early days of turbojet design were having problems with. It was getting the air compressed to the correct value and doing that while the incoming air might be of very turbulent flow. Military thrust, flight: 660 lbf (2.94 kN) at 17,200 rpm at altitude The compressor section was the big issue for everyone. Normal thrust, static: 1,160 lbf (5.16 kN) at 18,000 rpm at sea level Specific fuel consumption: 1.35 lb/lbf/hr (137.6 kg/kN/hr) Turbine inlet temperature: 1,500 ☏ (816 ☌) Maximum thrust: 1,360 lbf (6.05 kN) at 18,000 rpm at sea level Oil system: pressure spray at 40 psi (275.8 kPa) dry sump, 60 S.U. Production engines delivering 1,600 lbf (7.1 kN) thrust Increased mass flow version delivering 1,400 lbf (6.23 kN) at 18,000 rpm at sea level The primary application for the 19XB engine was the McDonnell FH-1 Phantom. The 19XB was used in the Gruman WTB3F-1, Douglas XB-42A (as auxiliary engines) and the Northrop X-4. The 1,600 lb thrust of the 19XB was achieved primarily by adding 4 additionnal axial-flow compressor stages.

This reconfigured engine was designated 19XB. Westinghouse submitted to the Navy a proposal for improving the performance and decreasing the weight of the 19B. The Northrop XP-79B was also powered by two 19Bs, but crashed on its first flight on September 12, 1945. The McDonnell XFD-1 Phamtom powered by two 19Bs made its first flight on January 26, 1945. The previous cannular combustion chamber was replaced by an annular one.įirst flight was made on 28 September 1944, using a JM-1 Marauder as a test-bed. The First engine with Variable IGV s was the GE J85. if the turbine wasnt burned up change the ignittors open the engine compressor cap to check there was no compressor damage change the filters and push her back out of the door. The layout of the compressor and turbine was similar to the 19A, but 4 extra stages were added to the compressor to give ten in all. Westinghouse J34-WE48 with No fan, Compressor and 2 stage turbine.
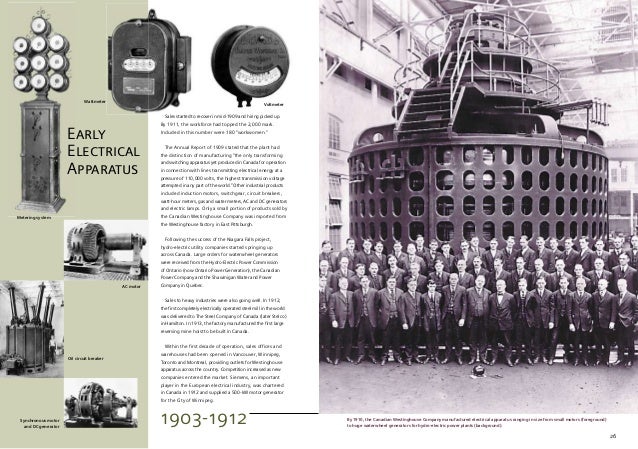
The 19B was to have a static thrust of 613 Kg (1350 lb) and be used as the main propulsion engine for an aircraft, rather than just a booster. It initially gave 1,200 pounds of thrust but improved to 1,600 in production versions. It was developed into the smaller J32, and the Westinghouse J34, an enlarged version which produced 3,000 pounds of thrust. On 21 January 1944 the second prototype was flown for the first time, under a Vought FG-1 Corsair. The static thrust developed being 515 kg (1,135 lb). On 19 March 1943, the first run was made. It had six axial stage compressor, a twenty four cannular combustion chamber and a single stage turbine. Design of 19A Yankee was begun on 10 August 1942.
